About Callan JMB
Learn about who we are, what we do, and stay up to date.
Emergency Preparedness & Response
Reliable, scalable, and proven solutions.
Specialty Packaging
A Shipping Story Beyond the Box
Products and Technologies
Innovation at Every Step: Callan JMB’s Products and Technologies
Fulfillment Services
Excellence Across Critical Industries
- Investor Center
- Contact Callan JMB
Creators of the Strategic National Stockpile Turn to Solving Global Shortages
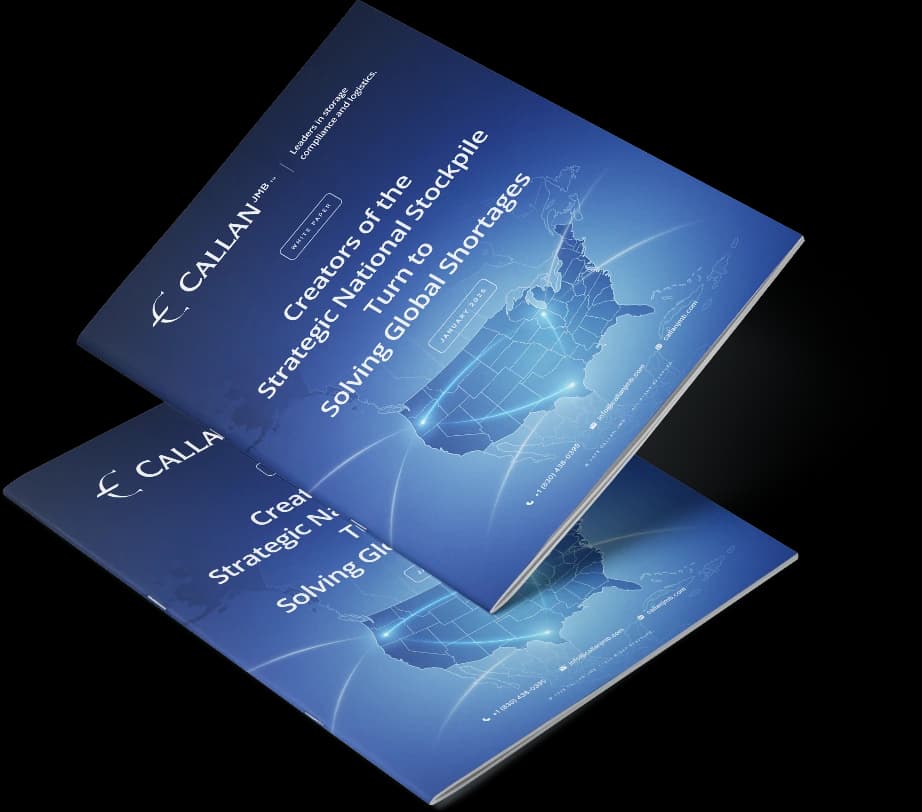
Callan JMB’s leadership were instrumental in developing the Strategic National Stockpile (SNS)* and its first sponsor-managed inventory facility and helped create a Vendor Managed Inventory (VMI) program to allow the City of Chicago to track subcontracted vendor-managed stockpiles of medical countermeasures (MCMs).
Their knowledge of federal government and pharmaceutical board storage and management regulations, their expertise in developing massive inventory management systems, and their experiences in cold chain logistics, including successfully distributing COVID-19 vaccines for the states of Texas, Oregon, Florida, and the City of Chicago, make them a perfect partner in a new push to solve the ongoing drug shortage crisis.
* Strategic National Stockpile (SNS) is the United States' national repository of antibiotics, vaccines, chemical antidotes, antitoxins, and other critical medical supplies and is part of the federal medical response infrastructure and can supplement medical countermeasures during public health emergencies.
The Issue
Shortages of critical life-saving medical countermeasures have had serious negative effects on the provision of health care in recent decades and are continuing to be a major issue.
For example, in 2024 Hurricane Helene caused a temporary shutdown of Baxter’s North Carolina IV bag manufacturing facility, which had provided 60% of the US IV solution supply. The second largest producer of IV fluids is B. Braun, who closed two of their Florida plants before Hurricane Milton hit.[1]
This was a wake-up call for the health care industry. The IV solution shortage has delayed surgical procedures and has led to triage decisions by hospitals having to prioritize care; more than 86% of healthcare providers across the country are affected by this IV fluid shortage.[2]
Other shortages have been endured in the last decade due to a wide variety of supply chain issues. Currently the FDA Drug Shortage database identifies 99 pharmaceuticals that are in shortage.[3] In 2023, 125 shortages were reported, 98 ongoing at the end of the year. There were 55 new shortages in 2023 and 53% of shortages were for generic sterile injectables. These drug shortages can last over three years: in 2023, 27 products were in shortage for over five years, and 6 for more than ten years. Moreover, the FDA helped to prevent 236 new shortages in 2023 that would otherwise have been included on the list.[4] These numbers show just how volatile the industry is and how difficult it is to resolve a shortage.
The causes of shortages are numerous, and the situation can devolve into a recurring cycle of shortage. The FDA tracks “discontinuances, GMP issues, increase in product demand, recalls, [and] supply interruptions” as responsible for shortages.[5]
Part of the problem is that even though the US produces finished drugs, the Key Starting Materials (KSMs) and Active Pharmaceutical Ingredients (APIs) are mostly imported.[6] If even one of the primary foreign producers of raw ingredients has a production or shipment issue, it can affect the entire US supply chain of finished products.[7]
Availability can be dependent on an array of unpredictable and uncontrollable events; the US Pharmacopeia identified “armed conflicts, political upheaval, trade disputes, animal diseases, degradation or contamination during transport, climate or other environmental conditions, or a decreased crop yield of plants that are a source of raw materials” as among the causes of shortages.[8]
For some drugs the finished product requires a complicated and specialized process or a dedicated facility, which increases manufacturing costs and reduces the ability to start new production lines.[9]
When only one or a few facilities are making a product, a shortage can be triggered by interruptions at those facilities because there is no backup readily available. If a drug’s formulation changes, equipment needs to be upgraded, or production volumes are reduced to fill a different shortage, a single supplier will not keep up with demand.[10]
The USP has identified four interrelated economic factors that are involved in shortages [11]:
- o low prices
- o complex processes
- o regulatory concerns
- o competition
A spike in the demand for a newly approved drug, especially generic products, can start a race to fill market share; the ensuing competition leads to low prices that are not economically viable for some producers. The more complicated processes in specialized facilities make it difficult for a business to justify the expense or expand to multiple facilities. When regulatory inspections identify GMP concerns that require changes to the line, the company may have to interrupt manufacture as well as pay to upgrade their systems. Any of these can cause a company to decide to discontinue a product.
The initial shortage of a drug, regardless of the chain of original causes, can sometimes be aggravated by attempts to resolve it. Protective purchasing of available supplies means less of the product is available to other users and when APIs are involved it can even lead to shortages in related products.[12]
When new producers step in to fill the production gap with generics, it can ultimately worsen the situation when the rush to manufacture leads to even more limited supplies of APIs, more cGMP citations for noncompliance, more revenue loss, and consequently more inevitable discontinuations.
This creates a headache for pharmacies who are trying to anticipate or endure shortages by increasing orders. Some do not have the storage capacity to withstand a lengthy shortage and do not want to purchase products that may expire before use. When a producer decides to discontinue the drug, finding an alternate supply can be difficult. A recent APSF article notes that “some pharmacy directors are considering buffering the inventory…of select medications/solutions that would typically cause patient delays or significant problems such as oncology treatments, surgeries, procedures and critical care needs.” A recent APSF article notes that “some pharmacy directors are considering buffering the inventory…of select medications/solutions that would typically cause patient delays or significant problems such as oncology treatments, surgeries, procedures and critical care needs.”[13]
No matter what the causes of the shortages are, “without significant market and policy interventions, current drug shortage trends will likely continue or worsen,” warns USP.[14]
It is clear that government intervention through easing import rules, expediting approvals, extending shelf lives, and postponing compliance deadlines for the duration of the shortage along with early warning reporting cannot solve the recurring cycle of shortages alone. Some have called for incentives for manufacturing reliability and quality, which may ease the financial concerns of companies who want to be sure they can recover their investment. But given that many shortages result from events beyond the control of producers and are not solely due to profit-and-loss considerations, advance planning and preparedness must be part of the solution.
The Solution:
VMI Stockpiles
What is needed is a US-based strategic stockpile and distribution system of vital MCMs that would be available under a Vendor Managed Inventory (VMI) program to be accessed during public health emergencies or events that cause interruptions in the normal supply chain.
The stockpiles will preclude the need for protective purchasing and hoarding by health care providers and allow continued use of just-in-time ordering that reduces storage burdens on these providers while ensuring a supply of unexpired, properly managed assets.
The AMA this year commented that “the IV fluid shortage underscores the need to additional action to build resiliency and redundancy into the domestic supply chain.”[15] Redundancy is key, which a strategic stockpile will support.
Creating strategic stockpiles for MCMs involves the acquisition of large warehouses in US locations not prone to natural disaster interruptions and in different areas of the US so that each facility can distribute to their assigned region quickly in emergencies and back up the other regions. Each facility must be able to handle domestic and international incoming shipments as well as outgoing transfers, including emergency distributions and cold chain shipments to anywhere in the US.
Each stockpile facility must be fully compliant with all regulatory requirements. The company must have written SOPs for all processes, protocols, and procedures that meet the strictest guidelines. MCMs must be stored at specific temperatures, so each facility must have ambient, CRT, refrigerated, frozen, and
ultra-cold storage units, all of which must be monitored continuously. Product manufacturer specifications (stacking limits, humidity ranges, for example) must be strictly followed. A complex inventory management system that tracks incoming and outgoing transfers, SKUs, quantities, and expiration dates is necessary with precise warehouse locations for each item stored. The IT systems must be secure and have built-in data archive redundancy.
Expert planning is needed to calculate the quantities to store at any given time. Soon-to-expire products must be reported and rotated, and the destruction of expired materials must be properly coordinated. In order to prevent excessive revenue loss from expired or unused products, a reliable purchasing network must be put into place.
Because of the extensive infrastructure that such an undertaking requires, there are few compliant and secure facilities that can create and manage strategic stockpiles under a Vendor Managed Inventory (VMI) program.
There are even fewer that have the qualifications to work with government agencies in this capacity. The realities of making it work can be complicated, whether the asset owner is the manufacturer or the government, or even a major healthcare system that wants to buffer its own supply chain. Making the process easier for all is having a contractor who can perform the storage and distribution of the stockpiles and be a go-between for the asset owner and product recipients.
Callan JMB has been successfully managing and distributing customer pharmaceutical assets, including government MCMs, since 2009 and sees strategic stockpiles of drugs in shortage and imminently entering shortage stage as an extension of what it already performs daily.
With its bonded, secure, fully compliant storage facilities in Texas, Oregon, and Illinois, it is ready to stockpile IV bags, sterile injectables, vaccines and other products identified as critical to the health care system. Callan JMB has relationships with major pharmaceutical manufacturers worldwide and is trusted with receiving their products responsibly. They have Wholesale Distributors Licenses for all states and the supply chain logistics know-how to ship cold chain materials from international sources into the US and to domestic end-users.
A VMI contractor for a government agency handling drug shortages would expect to receive notification of the immediate need for particular product transfers to specified locations and would prepare, pack, and ship the products within a 24-48 hour window. Callan JMB had experience doing exactly this during the COVID-19 and MPOX pandemics in Texas, Oregon and Illinois. In addition to having fully operational facilities in each of these states, they have expert personnel to manage these transfers, access to major carriers, an extensive network of trained couriers, and specialized cold chain shippers that maintain required temperatures for as long as the shipment will be in transit.
Callan JMB has an excellent track record of serving government agencies in Emergency Preparedness and Response, including Texas Department of State Health Services (DSHS), Oregon Health Authority (OHA), and the City of Chicago’s Department of Public Health (CDPH) and Office of Emergency Management and Communications (OEMC), as well as providing specialty shippers to the Defense Logistics Agency (DLA).
Callan JMB’s CEO, COO and CIO have all worked previously for the CDC and were instrumental in establishing the Strategic National Stockpile (now under ASPR). Their combined expertise in supply chain logistics, thermodynamics, biologics, inventory management, and compliance is unparalleled in the industry. Callan JMB’s CEO is a key subject matter expert for the SNS and other government agencies planning their emergency preparedness programs and can identify and acquire the most critical products for a VMI stockpile.
No company is better positioned than Callan JMB to immediately step in to set up and manage national stockpiles of MCMs and help minimize the effects of future shortages.
Callan JMB is an integrative logistics company empowering the healthcare industry and emergency management agencies through exceptional fulfillment, storage, monitoring, and cold chain logistics services to secure medical materials and protect patients and communities with compliant, safe, and effective medicines.
ENDNOTES
- [1], [2], [13] Anesthesia Patient Safety Foundation. The Sterile Intravenous (IV) Fluid Shortage Crisis Update. Patricia A. Meyer and Russell K. McAllister. November 15, 2024.
Accessed on 12/10/24.https://www.apsf.org/article/the-sterile-intravenous-iv-fluid-shortage-crisis-update/ - [3] Federal Drug Administration. FDA Drug Shortages.
Accessed on 12/10/24. https://dps.fda.gov/drugshortages - [4], [6], [9], [11], [12], [14] US Pharmacopeia. USP Annual Drug Shortages Report: Economic factors underpin 2023 shortages. June 2024.
Accessed on 12/10/24.https://www.usp.org/news/us-drug-shortages-reach-decade-high-and-last-longer - [5] Federal Drug Administration. Drug Shortages. 10/03/24.
Accessed on 12/10/24.https://www.fda.gov/drugs/drug-safety-and-availability/drug-shortages - [7], [8], [10] Pharmacy & Therapeutics. The Drug Shortage Crisis in the United States: Causes, Impact, and Management Strategies. C Lee Ventola. P T. 2011 Nov; 36(11) 740-742, 749-757.
Accessed 12/11/24.https://pmc.ncbi.nlm.nih.gov/articles/PMC3278171/ - [15] AMA. Fixing IV fluid shortage only a start in addressing drug supply. Kevin B. O’Reilly. Oct 30, 2024.
Accessed 12/10/24.https://www.ama-assn.org/delivering-care/public-health/fixing-iv-fluid-shortage-only-start-addressing-drug-supply